From Stranger Things to the Top Gun sequel, nostalgia for the 1980s has been a prominent feature of popular culture recently.
One of the decade’s iconic TV series was Knightrider (1982-1986), in which crimefighter Michael Knight is assisted by KITT, a supercomputer on wheels so advanced it can think and learn by itself and even communicate with humans. What seemed like science fiction forty years ago seems normal today. The sheer complexity of today’s answer to KITT is staggering, with standard features ranging from driver alertness monitoring and cabin environment controls to lane departure warnings, tyre pressure alerts and cutting-edge wireless entertainment systems, to name just a few. The average vehicle can have up to 50 central processing units (CPUs) controlling these functions, with some CPUs operating independently of each other.
Each year, increasingly tech-savvy consumers are wooed with models which are smarter than before. This level of sophistication is likely to rise further as the prospect of self-driving vehicles moves closer. In particular, the critical role of semiconductors will continue to expand in all areas of the car, ranging from navigation, diagnostics and communications to comfort, entertainment and safety. By 2030, electronic systems powered by semiconductor-based chips could comprise up to 50% of the cost of a new car.
Running parallel with this exponential growth in computerised complexity is the move to electric vehicles (EVs). Although in part driven by the expectations of eco-conscious consumers, the switch to EVs will increasingly also be mandated by law. In August 2021 – with executives from leading US automakers looking on – President Biden announced a target for half of all cars sold in the United States to be zero-emission vehicles by 2030. In June 2022, the EU Parliament voted in favour of reducing CO2 emissions from new cars by 55% by 2030 and 100% by 2035. This would effectively make it impossible to sell fossil-fuel powered vehicles in the EU. As well as regulatory pressure, governments are using a carrot and stick approach of subsidies and carbon taxes to incentivise EV use.
These two megatrends – the computerisation of cars and the transition to EVs – are driving a paradigm shift in the automobile landscape. The increased use of advanced technology means that traditional line production operations are being replaced. Instead, modular production methods feature specialist teams coming to the car to work on it at different stages of its construction. There will inevitably need to be a massive expansion and investment in public EV charging stations. According to a recent industry report, the global EV charging station industry was worth $16.6 billion in 2021 but this is expected to increase almost fourteen-fold to $226.3 billion by 2031.
Supply chains will need to adapt accordingly, but this transition is facing major challenges. Manufacturers in North America and Europe have been unnerved by the acute supply chain disruption witnessed in recent years, be that the war in Ukraine, the increasing costs of transportation or ships blocking the Suez canal. There is also mounting concern at China’s monopoly of the materials needed for EV battery production, with Beijing accounting for 85% of the world’s rare earth metals and two thirds of scarce metals and minerals. Continued tension over Taiwan is also a worry, not least given the critical role the latter plays in semiconductor production.
There is therefore a major focus on reshoring production and shortening supply chains. In 2021, Ford and South Korean manufacturer SK Innovation announced plans to spend over $11 billion building EV battery factories in Tennessee and Kentucky and one of Joe Biden’s first acts as President was to order an urgent supply chain review. The CHIPs for America Act aims to incentivise semiconductor production and the California-based Mountain Path mine is the focus of a renewed US strategy to fully reshore the rare earth supply chain. There may also be a long-term focus on finding a substitute for rare earths, or even retooling products so that rare earths are no longer required. BMW has started producing EV batteries that do not require rare earth metals and Toyota and Volkswagen are striving to reduce their rare earth reliance.
Aspects of production are also moving back towards Henry Ford’s vertically integrated model of making every car component inhouse. Elon Musk has been leading the way here, with Tesla spurning the traditional “engineering catalogue” approach of buying off the shelf parts from suppliers in favour of designing and building as much as possible itself. This is all part of having greater control of supply chains, even extending to the mines where critical minerals are sourced.
The reality is that reshoring will take time to bear fruit and developing inhouse production capabilities and expertise will not happen overnight. Another stumbling block is the fact that the critical infrastructure needed for the EV revolution is sorely lacking. Many consumers are certainly keen to buy hybrid or EV vehicles but are dissuaded by the dearth of charging stations outside of urban centres. Charging stations that are available often prove inoperable or are too slow. There are also safety concerns, particularly among female EV users who can feel vulnerable using isolated charging stations at night. In the UK, there have been calls for minimum personal safety standards to be introduced, with requirements for EV charging stations to be well-lit with monitored CCTV cameras and emergency contact buttons.
In the meantime, from an inventory management perspective there will be a continued focus on storing buffer stock on a Just in Case basis. During this transition phase, Original Equipment Manufacturers (OEMs) will need to have a high availability of inventory to avoid negative impacts on revenues. Their Tier One and Tier Two suppliers will need to adapt accordingly and ensure they have enough of the right inventory on standby to cater to supply chain disruption and fluctuations in demand. OEMs will inevitably be dictating stricter buffer stock requirements in their supplier agreements, with manufacturers insisting on greater aftermarket inventory for both combustion and EV models.
Maintaining high levels of buffer stock may foster greater supply chain security, but it does bring with it significant downsides, notably a high Days Inventory Outstanding (DIO) number and a sluggish Cash Conversion Cycle. Corporates want the agility and liquidity to pursue their strategic goals, not be held back by asset-heavy balance sheets and trapped capital. This is a problem.
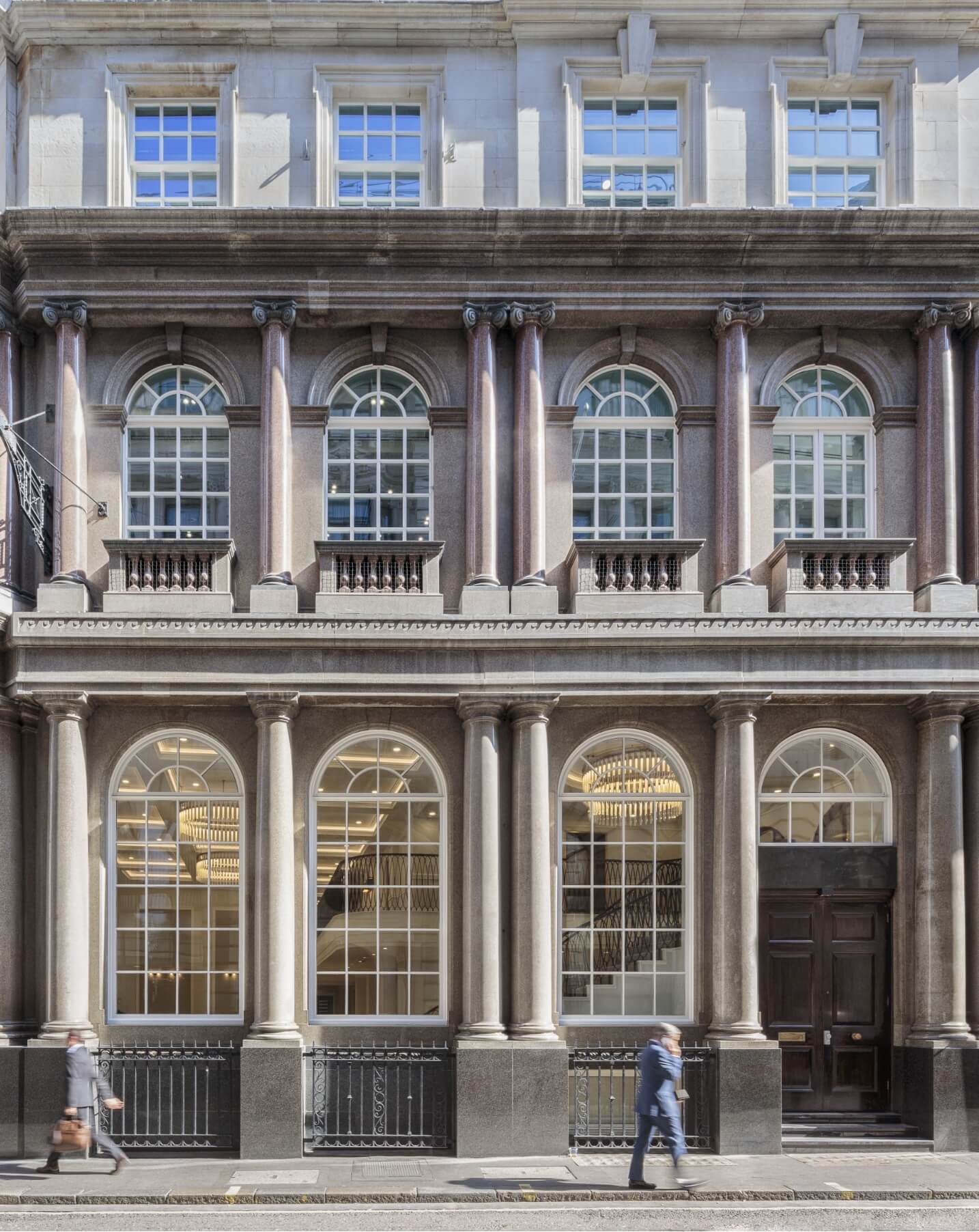
Falcon can help.
We can lighten the load on balance sheets and support companies with third-party inventory ownership during this period of industry transition. We achieve this by purchasing inventory from suppliers and providing goods to customers on a Just in Time basis. Falcon’s solutions mean we can offset the increase in inventory and help to optimise and de-risk supply chains over time.
The paradigm shift in the automobile industry is happening. As with most change, there will be some pain and discomfort. Fortunately, Falcon’s solutions mean that working capital and liquidity do not have to be sacrificed for security as you navigate this changing landscape. We can help you achieve both.
This article has been prepared solely for information purposes and the opinions expressed and set out herein are illustrative only. Please note that any content in this article is based upon Falcon’s own views and opinions and should not be relied upon by the reader as advice. Falcon shall not be liable for losses arising out of reliance on this article. For more information, please contact [email protected]